A few years back, Amazon was slapped with a major fine ($872,000, to be exact) for violating shipping standards for hazardous materials. The price tag is shocking, but not as shocking as the level of danger those violations could cause. After all, when packaging dangerous goods, noncompliance can harm more than just your business.
In Amazon’s case, a package sent from Florida to Illinois was found to contain ethanol, a highly flammable liquid. The package had started leaking during transit. Upon investigation, it was found that the package lacked the correct markings and was missing required paperwork (which was supposed to include emergency response information).
I don’t know about you, but seeing the rate at which eCommerce moves, I think compliance is a huge deal. While this is one example, industries such as chemicals, life sciences, and even heavy industries must deal with packaging regulations when it comes to dangerous goods.
That’s why we’re sharing our top 5 tips to help ensure you safely and successfully package dangerous goods.
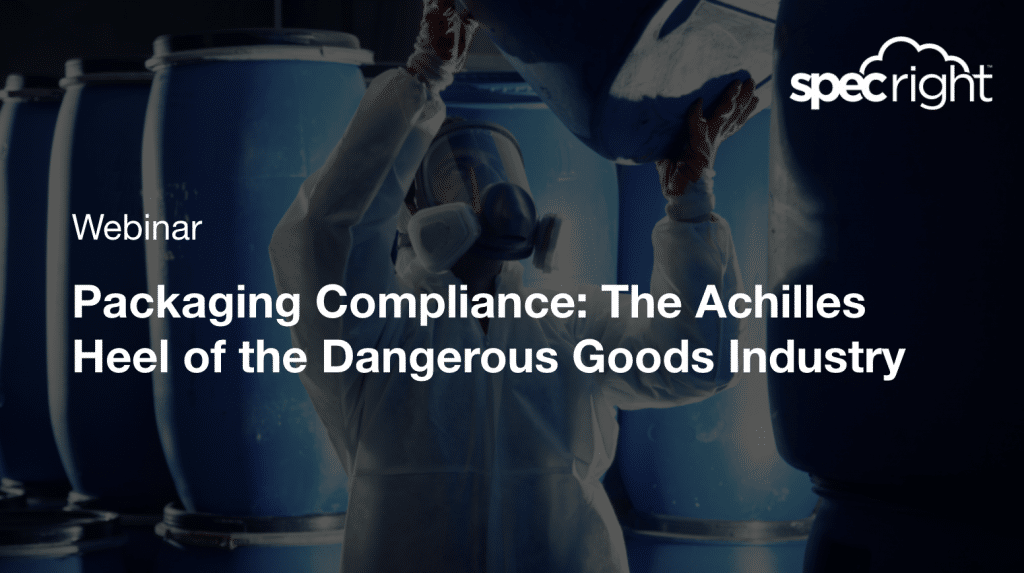
1. From Goods to Supply Chain Conditions, Know What You’re Dealing With
First things first, you need to know what kind of dangerous good you’re dealing with. According to the United Nations, there’s 9 general classifications of dangerous goods, with up to 15 subcategories. There’s also different requirements for the type of transport you plan to use. It’s crucial to do the initial research and fully understand what type of packaging and labeling is needed to prevent fines and accidents later on.
Luckily, technology can help so you don’t have to do as extensive research every time.
Although, research doesn’t stop at the standards. Note that regulatory compliance is the minimum standard. Packaging specifications must be based on the principle of “fitness for purpose”. If supply chain conditions cause your packaging to fail, resulting in an incident, simply saying that it was UN certified will not be a strong enough defense in court.
For example, an 0.8mm steel drum can be UN certified. If you plan on sending it on a 5,000 mile journey across Europe into the heart of Russia for example, where not all roads are paved smoothly, it could fail at the bottom seam through excess vibration. In this scenario, the liability is on you.
Our advice? Know what you’re dealing with!
2. Digitize Everything
Start building your digital knowledge repository, so you don’t have to start from scratch each time you have a hazmat (hazardous material) on your hands.
Begin by digitizing product specs and linking those specs to all related regulatory compliance documents and requirements. This way, you have everything you need when you start designing your package. With a digital thread in place, it’s easy to clone specs, as well as access and search data. Not only does this save you time, but it ensures no crucial data slips through the cracks.
When I was a packaging engineer dealing with hazardous goods, I remember auditing a facility in another country and knowingly instantly that we were out of compliance. It was a terrible feeling - after all, I was the global packaging manager - why didn’t I have visibility into packaging across facilities?
During COVID-19, in-person audits and travel have been further restricted, which makes having digitized packaging specifications even more important.
3. Stay Ahead with Document Control and Versioning
One of the biggest problems we see has to do with how often product and packaging specifications change. And in this day and age, they change a lot.
This leads to version control issues and causes stakeholders to act on incorrect data. And in the case of dangerous goods, you wouldn't want to end up with an ill-fitting or non-protective package.
Luckily, this is easy to overcome using Specification Management software. If a spec changes, you’ll know immediately. Always have access to the most up-to-date data and stop spending time chasing specs.
Your suppliers can also be granted access rights to the specs they supply. This maintains a single source of truth for specs and gives suppliers the responsibility to validate that “what you specify is what you get”.
Clarifying this responsibility for the supplier and formally tying it to agreements can help avoid unauthorized changes. This shouldn’t happen regardless, but it can and it does. As a packaging engineering manager, I’ve even seen a supplier of UN certified rigid plastic packs swap out the approved resin for post consumer recyclate when supplies were short. This went against all regulations and was only discovered by a site audit. And this was the incident I knew about - it made me realize how important visibility is across the packaging value chain.
4. Automation, Automation, Automation
My next tip is to automate everything you possibly can. A best practice I recommend is to tie an alert to any product classified as a dangerous good. For example, if you have a product containing isopropyl alcohol, an alert should come up stating that the product is classified as a dangerous good and which specs you can refer to for regulatory compliance information.Companies that ship dangerous goods should have a formally qualified safety advisor, but as we’ve seen, that’s often not enough.
Checks and balances can be readily built into a spec management system. Linking products to specifications and transport classifications, packaging groups, markings and labelling requirements, to help maintain compliance.
In the US the DOT (Department of Transportation) can, and does, audit locations filling, handling and shipping dangerous goods. Ensuring specs are accurate and any changes are fully documented is vital.
Specification Management produces an audit trail of who changed what, where and when, automatically.
5. Increase Visibility for Crucial Stakeholders
The final step is to ensure visibility across the supply chain. With products of this caliber, there’s a lot of people to answer to. Make sure you've got the right data in the right hands at the right times. This means giving access to data across your internal teams and with your external partners and suppliers.
It’s crucial to ensure that all stakeholders are looking at the same specs, as it helps prevent assumptions and incorrect or unauthorized decisions.
With Specright, you can do all of this and more. As the first purpose-built platform for Specification Management, we help companies increase visibility, collaboration, and efficiency.